La préfabrication : en quoi cela consiste ?
Très courante dans la construction bois, cette technique de construction consiste à fabriquer en atelier des éléments constitutifs qui seront ensuite assemblés sur chantier pour former le bâtiment. À l’heure actuelle, la préfabrication concerne essentiellement des « sous-ensembles » bidimensionnels (pans de purs, planchers, éléments de toiture…). On parle dès lors de préfabrication 2D. En la matière, les entreprises de construction bois sont clairement à la pointe : la fabrication des éléments est ultraprécise et intègre, outre la structure même, des composants supplémentaires (isolations, menuiseries extérieures, parements…).
La préfabrication 3D, développée depuis quelques années par une série d’entreprises de construction bois, va un pas plus loin : cette fois, ce sont des modules 3D entièrement finis qui sont assemblés en atelier et ensuite simplement transportés et posés sur site. Ces modules complèts intègrent les techniques (eau, électricité, chauffage…), mais aussi des finitions et aménagements intérieurs (sanitaires, cuisine, placards…).
Le bois, idéal pour la préfabrication 3D
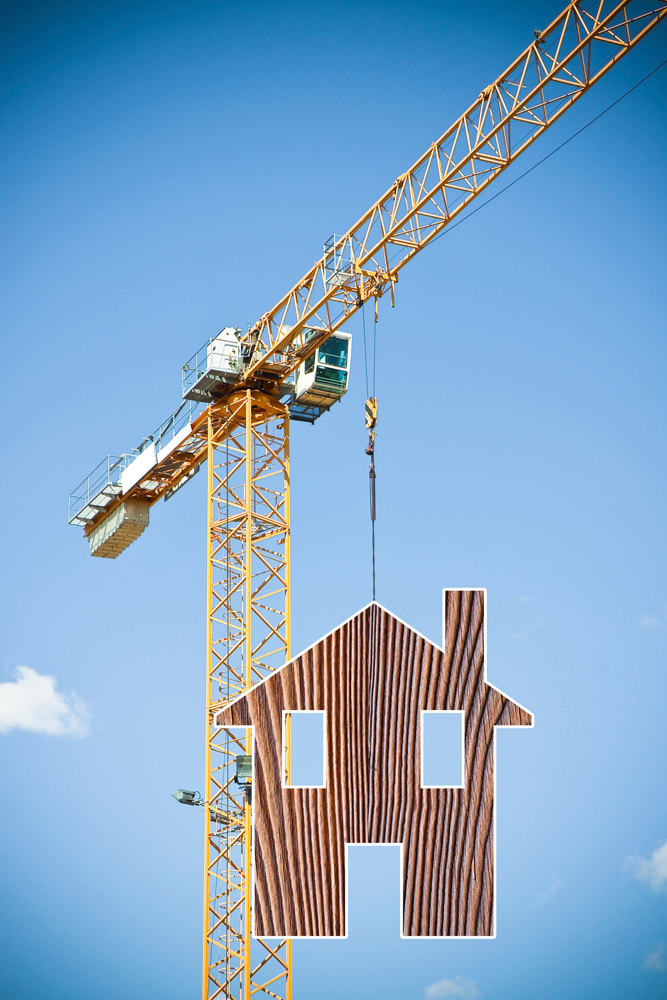
Puisque les modules sont transportés par camion en posés et manipulés sur site par des grues, ils doivent être aussi légers que possible. L’avantage du bois pour la préfabrication 3D tient donc essentiellement à sa légèreté. Les structures sont généralement en ossature remplie d’isolant.
Les matériaux de parement doivent, eux aussi, être légers et souples pour éviter les fissures lors des manipulations. Le parement le plus courant est le bardage en bois. Si le client souhaite un parement en pierres ou en briques, celui-ci devra être placé sur chantier et il faudra prévoir des fondations traditionnelles en béton.
Les avantages de la préfabrication 3D
Des délais de construction raccourcis
- Le chantier n’est jamais interrompu suite aux caprices de la météo.
- Le planning d’interventions des différents corps de métiers est plus facile à réaliser et à respecter.
- Grâce à l’extrême précision de la préfabrication, les châssis peuvent être commandés sur plan.
- Plusieurs modules d’un même logement peuvent être fabriqués parallèlement.
- De même, les travaux préparatoires sur site (fondations, aménagements extérieurs, raccordements aux impétrants) peuvent être réalisés en même temps que la préfabrication des modules en atelier.
- L’assemblage des modules sur site peut être réalisé en une seule journée. Il faudra compter maximum 3 jours supplémentaires pour parfaire les jonctions entre modules et réaliser les raccordements des techniques, des impétrants et les connexions au niveau des étanchéités.
Précision et qualité
- Le processus de fabrication est optimisé et ne laisse aucune place à l’improvisation.
- Le bureau d’étude et les équipes en atelier sont en interactions permanentes, pour un suivi très rigoureux à chaque étape.
- L’environnement de travail en atelier est contrôlable. Il en résulte que les matériaux sont soumis à des conditions optimales constantes (le bois, par exemple, ne sera pas soumis à la pluie).
Plus de sécurité et de confort pour les ouvriers
- Ni trop chaud, ni trop froid, ni trop humide… Le travail en atelier permet aux ouvriers de travailler plus confortablement et de se concentrer sur la qualité et la précision.
- Parce que les procédures de sécurité sont plus faciles à mettre en place et à systématiser en atelier, le cadre de travail est également plus contrôlé et permet de limiter les risques d’accident.
Un impact environnemental très faible
- En raison de leur légèreté, les modules préfabriqués ne nécessitent pas d’importants travaux de fondation. Généralement, ils sont posés sur des pieux vissés en acier galvanisé ou sur des plots de fondation. Ce système permet de conserver la réversibilité des terrains : concrètement, les modules peuvent être enlevés aussi facilement qu’ils sont été installés et le terrain est alors ramené à son état d’origine.
- L’utilisation précalculée de la moindre ressource permet de limiter drastiquement le risque de gaspillage et de déchets. En outre, la collecte des déchets générés par la fabrication des modules est centralisée dans l’atelier, ce qui facilite leur valorisation comme produits connexes ou via une filière de recyclage.
Inconvénients et limites
Des modules de taille limitée
Les principales contraintes de la préfabrication 3D sont liées au transport des modules par camion, qui impose des dimensions limitées. À partir de modules de 12 mètres de long, il faudra faire appel à une entreprise de transports exceptionnels bien entendu plus onéreuse pour l’acheminement sur chantier.
C’est la raison pour laquelle la préfabrication 3D s’est jusqu’ici principalement développée grâce au marché de logements touristiques qui sont des habitats de plus petites dimensions. Elle est aussi souvent utilisée pour réaliser des extensions, ou des petits bureaux professionnels. Néanmoins la préfabrication 3D permet aussi de construire des maisons, réalisées grâce à l’assemblage de plusieurs modules, sur un ou plusieurs étages. C’est la construction de grands espaces ouverts qui, aujourd’hui, reste globalement hors de portée de la préfabrication 3D.
Moins de souplesse en cours de construction
Une fois que les modules sont en production, toute modification sur le projet devient extrêmement difficile. Heureusement, les outils de modélisation et de visualisation 3D permettent au client d’avoir un aperçu très précis et abouti des différentes pièces de sa future habitation durant la phase d’étude du projet.
Cet article s’inspire un vaste dossier publié au 4e trimestre 2021 dans “Les Infos de RND”. Pour consulter ce dossier, cliquez ici.